When making an electronic product housing, many factors need to be considered to ensure the quality and function of the plastic injection parts. Because the electronic product shell is not only to play a beautiful role, but also to protect the internal electronic components from the influence and damage of the external environment. This article will cover some of the key details to be aware of when making an electronic plastic cases.
1. Material selection: When making electronic product shells, we must first consider the choice of plastic materials. Plastic materials such as engineering plastics and electronic silicone are usually selected, which are characterized by drop resistance, climate change resistance and suitable thermal conductivity. The plastic cases of the microelectronics product is made of metal materials, such as aluminum, zinc and aluminum alloy, in order to effectively heat dissipation. 2. Plastic injection parts design: The design of the plastic shell needs to pay attention to the mechanical structure and spatial layout. The first step is to choose the right size and shape to suit the specific electronic components. Taking into account the user's feel and human experience, the shell shape should conform to the ergonomic principle. In addition, the keys, interfaces and arrangements on the shell should be reasonably arranged so that users can easily operate the equipment. 3. plastic injection shells processing: Some details of shell processing can directly affect the quality of the plastic product. One of the most important is the surface treatment process, you can choose spray paint, ink printing and other ways to customize personalized patterns. Pay attention to the processing of holes and openings on the housing to ensure accurate correspondence with internal electronic components. The high-precision hole position machining and cutting process in the processing process should be operated by advanced processing equipment and procedures.
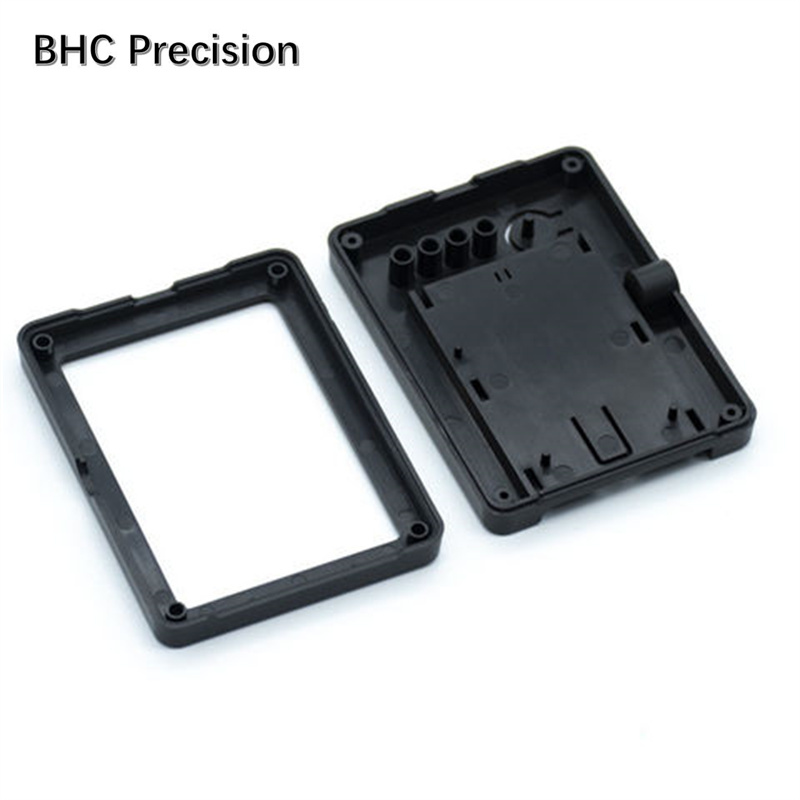
When making the plastic cases of electronic products, reasonable material selection, careful shell design and shell processing are crucial. Only after taking these factors into account, can we make a beautiful appearance, normal function and meet the needs of the user's electronic plastic product shell. In the future development of the plastic electronic product market, more attention to innovation and personalized plastic electronic product enclosures will become the mainstream. Providing good shell solutions will help enhance the image of the company and the brand, and meet the needs of different users.